Quèsaco un matériau composite ?
Les matériaux composites envahissent les structures des transports et des bâtiments à mesure qu’ils séduisent les chercheurs. Leurs qualités épatent, et ils s’imposent comme incontournables pour faire face aux défis environnementaux à relever : diminution des émissions de gaz à effet de serre, constructions plus résistantes et plus durables… Comment ces matériaux sont-ils conçus ? Pourquoi sont-ils autant prometteurs ? Sylvain Drapier, chercheur à Mines Saint-Étienne sur le sujet, répond à ces questions pour ce nouveau Quèsaco dédié aux matériaux composites.
Le principe d’un composite, c’est d’être constitué de deux matériaux différents ?
Sylvain Drapier : Disons d’au moins deux matériaux. Pour bien comprendre, il est plus facile de raisonner en fraction volumique, c’est à dire en proportion de volume que chaque constituant occupe dans le composite. En général, un composite contient entre 40 et 60 % de renforts, souvent sous forme de fibres. Le reste est constitué d’un liant, appelé matrice, permettant d’agréger ces fibres. De plus en plus, la fraction de liant est légèrement diminuée de l’ordre de quelques pourcents pour ajouter ce que nous appelons des charges additionnelles, comme des minéraux par exemple, qui vont optimiser les propriétés finales du composite.
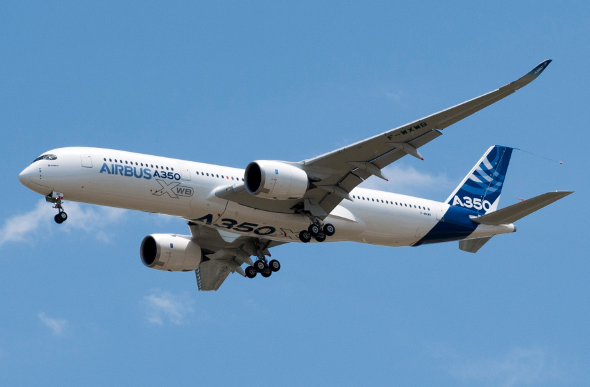
50 % de la structure de l’Airbus A350 est en composite. Le secteur des transports est particulièrement intéressé par ces matériaux.
S’agit-il de fibres identiques à celles de nos vêtements ?
SD : Les composites biosourcés utilisant des fibres naturelles comme le lin ou le chanvre émergent. De ce point de vue, c’est un peu ce que nous retrouvons dans nos vêtements. Mais ces matériaux là restent encore rares. Pour les composites fabriqués et diffusés à grande échelle, il s’agit plus de courtes — voire très courtes — fibres de verre. Pour donner un ordre de grandeur : elles ont un diamètre de 10 micromètres et sont longues de 1 à 2 millimètres. Elles peuvent être plus grandes pour des produits qui doivent reprendre des efforts limités, comme les planches à voile ou les coffrets électriques par exemple, dans lesquelles les fibres mesurent quelques centimètres de long. Les matériaux haute performance demandent en revanche des fibres continues atteignant plusieurs centaines de mètres, enroulées sur des bobines. C’est le cas des fibres d’aramide dont la plus connue est le Kevlar, des fibres de verre avec lesquelles sont fabriquées les pales d’éolienne, mais aussi des fibres de carbone utilisées dans les structures très fortement sollicitées telles que les vélos, voitures haut de gamme, avions, …
Suffit-il de lier ces fibres en les trempant dans de la colle pour élaborer un composite ?
SD : Tout part de réseaux de fibres, en 2D ou en 3D, élaborés par des sociétés spécialisées. Il s’agit alors véritablement de textiles tissés, voire tricotés dans le cas de pièces de révolution. À partir de là, il existe plusieurs voies d’élaboration. Certains procédés consistent à faire pénétrer de la résine plastique sous forme liquide dans ce réseau de façon à lui donner du liant. En chauffant, la résine se durcit : nous disons alors qu’elle est thermodurcissable. D’autres résines polymères sont utilisées à l’état solide et fondent en chauffant, elles remplissent les espaces entre les fibres, et se solidifient lorsque le matériau est ramené à température ambiante. Il s’agit alors de matrices dites thermoplastiques, constituées de la même famille de polymère que celle des produits plastiques recyclables de notre quotidien. Il existe également des matrices métalliques ou céramiques, mais c’est plus rare.
Par quoi le choix de la matrice et des fibres est-il guidé ?
SD : Tout dépend de l’usage. Les matrices céramiques sont utilisées pour des composites insérés dans des structures chaudes ; les résines thermoplastiques fondent en effet au-delà de 200-350 °C, et les thermodurcissables se fragilisent au-dessus de 200 °C. Certaines utilisations demandent vraiment des choix de matrices atypiques. C’est le cas des freins pour Formule 1 ou des tuyères de la fusée Ariane qui sont conçus en carbone 3D : non seulement la fibre est en carbone, mais le liant également. Par rapport à une pièce en carbone simple, ce composite est bien plus résistant à l’effritement, et peut être sollicité à des températures dépassant largement les 1 000 °C.
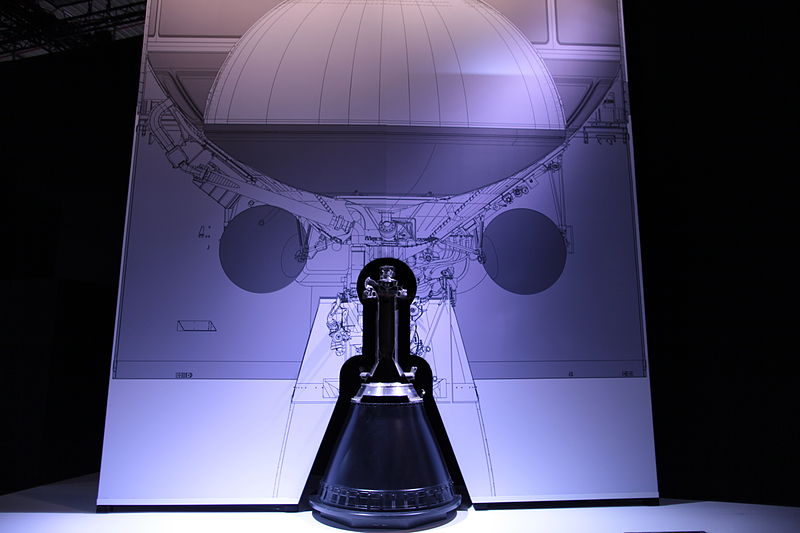
Le moteur Vinci est destiné aux fusées de l’agence spatiale européenne. Sa tuyère (le cône ici en noir) permettant la propulsion est conçue en composite carbone-carbone. Crédits : DLR German Aerospace Center.
Quels sont les avantages des composites ?
SD : Ces matériaux sont très légers tout en offrant des propriétés physiques au moins équivalentes à celles des matériaux métalliques. C’est ce qui séduit beaucoup le secteur des transports puisqu’un véhicule moins lourd consomme moins d’énergie. Les composites ont aussi l’avantage de ne pas rouiller. Autre particularité : nous pouvons intégrer des fonctions à ces matériaux. Par exemple, nous pouvons rendre un composite plus souple à certains endroits en orientant les fibres différemment, ce qui peut permettre de remplacer des sous-ensembles de pièces par une seule. En revanche, les résines des composites sont souvent sensibles à l’eau. C’est pour cette raison que l’aéronautique simule des cycles de vieillissement dans des conditions d’humidité et de température spécifiques.
Comment le recyclage des composites est-il envisagé ?
SD : Les matrices thermoplastiques peuvent être fondues. Les polymères sont alors séparés des fibres et chaque constituant est traité séparément. Par contre, les matrices thermodurcissables n’ont pas cet avantage, et les composites qui en sont constitués doivent être valorisés autrement. Mais c’est justement pour avoir des matériaux dont l’empreinte carbone est réduite que les chercheurs se tournent vers les composites agrosourcés, en utilisant de plus en plus de fibres végétales. Il existe même des composites 100 % agrosourcés, qui associent à ces renforts biologiques des résines polymères biosourcées. La problématique du recyclage des composites n’occupe pas encore la place qu’elle devrait avoir, mais actuellement les équipes de recherche s’investissent de plus en plus dans cette voie de développement.
En savoir + sur les composites agrosourcés
En savoir + sur les travaux de Sylvain Drapier
Trackbacks (rétroliens) & Pingbacks
[…] fibre de verre qui sert de renfort dans les matériaux composites est fabriquée à partir d’un mélange de silice et de différents autres composants comme […]
[…] En partenariat avec les fabricants de matériaux, équipementiers et constructeurs de la filière automobile, les équipes de recherche d’IMT Nord-Europe étudient le déploiement et la mise en œuvre des matériaux polymères et composites dans les véhicules. Actuellement, ces matériaux représentent environ 20 % de la masse d’un véhicule. Leur proportion peut être augmentée à condition de satisfaire un cahier des charges exigeant, et inchangé en matière de sécurité et de performance. « Dès lors qu’une pièce ou un composant est allégé, ce composant, comme le véhicule, est soumis aux mêmes batteries de tests et protocoles d’homologation », explique Patricia Krawczak, enseignante-chercheuse à IMT Nord-Europe, spécialisée dans les polymères et composites. […]
[…] de ces biomasses aux cycles thermiques parfois élevés qui leur sont appliqués avec des matrices thermoplastiques – ou encore leur composition […]
[…] des branches d’arbres peut par exemple se faire en transformant celles-ci en renforts pour matériaux composites, qui peuvent ensuite être utiles dans le secteur du bâtiment pour fabriquer le platelage ou des […]
[…] « Cela favorise le développement de micro-organismes comme les bactéries et les champignons filamenteux, qui assurent la dégradation de polymères naturels, comme la pectine et l’hémicellulose, liant les fibres entre elles au sein des tiges », poursuit le chercheur. Anne Bergeret, également chercheuse à IMT Mines Alès, et spécialisée quant à elle dans le domaine des matériaux polymères et composites, précise l’intérêt de cette étape : « La séparation des fibres de l’écorce de la tige est alors facilitée lors de l’étape suivante appelée ‘teillage’. » La fibre longue teillée est ensuite peignée, avant d’arriver en filature pour produire un textile, qui servira de renfort pour l’élaboration d’un matériau composite. […]
[…] À lire sur I’MTech : Quèsaco un matériau composite ? […]
[…] avec des matériaux et procédés classiques, les constructeurs ont de plus en plus recours aux matériaux composites. Or les composites sont produits avec des techniques qui rappellent l’impression 3D. Les coupler […]
[…] l’association de plusieurs techniques pour faire du diagnostic de l’intégrité structurale de pièces composites en fonctionnement. Là, les industriels ont commencé à être vraiment intéressés, séduits par […]
[…] À lire sur I’MTech : Quèsaco un matériau composite ? […]
[…] de la métallurgie intéressent entreprises et industriels. Et ce, malgré l’essor parallèle des composites. Anna Fraczkiewicz n’y voit d’ailleurs pas de concurrence, mais un équilibre dynamique […]
[…] À lire également sur le blog : Quèsaco un matériau composite ? […]
[…] À lire également sur le blog : Quèsaco un matériau composite ? […]
[…] En savoir + sur les matériaux composites […]
[…] Quèsaco un matériau composite ? […]
Laisser un commentaire
Rejoindre la discussion?N’hésitez pas à contribuer !