Recycling concrete and sediment to create new materials
How can we meet the needs for construction materials in an environmentally responsible manner? Recycling could be the solution, but it is not yet easy to create high-performance and eco-friendly materials using waste. At the conference on Natural Resources and Environment, which took place on November 5-6 2014 at Institut Mines-Télécom, Vincent Thiéry, a researcher at Mines Douai, presented two aspects of the research developed in the Civil and Environmental Engineering department on designing the concrete of the future.
It is increasingly difficult to find high-quality raw materials to make materials like concrete. At the same time, we are generating more and more waste that we do not know how to dispose of – industrial by-products, concrete from building renovations or demolitions, and sediments that block ports and canals. Vincent Thiéry and his colleagues are therefore working to design alternative materials, such as concrete and cements, using these new raw materials whose potential remains unexplored: “One the one hand, we could generate less waste, and on the other hand, we wouldn’t have to use as many natural resources.”
Recycling sediments and old concrete
“Our mission is to create high-performance materials that are environmentally friendly. This can be accomplished through recycling, by incorporating a certain amount of waste into these materials.” The sediments are retrieved by dredging ports and canals every 10 to 20 years, which produces large quantities of materials. The construction materials sector is has many uses for the recovered sediments: “We will try to integrate them into the construction of roads, prefabricated concrete (casting of concrete blocks or concrete for street furniture), landscaped mounds, embankments, and in artificial aggregates for reinforcing beaches.” Another possibility is recycled concrete aggregate. 300 million tonnes of construction and demolition waste are generated each year, which can be reused as aggregate for producing concrete, even though this type of aggregate requires much more water than traditional concrete. Better yet, “certain industrial by-products and waste – typically those generated by the steel industry – are resources used in the cement industry: the integration of these materials can produce attractive results, such as resistance to seawater and good mechanical strength.”
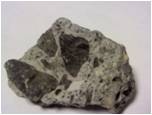
Recycled concrete aggregate (diameter: approximately 1 cm). Black components: a natural aggregate. Gray components: cement paste. These two components behave differently when they are integrated into new concrete; they must be correctly characterized and quantified.
Recycling challenges: sustainable formulations
“Scientific and technical challenges arise in relation to durability.” The dredged sediments contain heavy metals and organic pollutants, which must not be released into the environment: therefore, the stabilization of the recycled materials must be ensured. “Concrete that is poorly made can develop certain pathologies — which appear in the form of swelling, flaking, or crumbling — and can no longer be used for its intended purpose.” A very well known pathology – the alkali-silica reaction – has been one of the Civil and Environmental Engineering (GCE) department’s areas of expertise for around fifteen years. Not all types of aggregate cause this pathology, yet for some of them, a specific mineralogy must undergo extensive analysis to ensure it will not react. “Eventually, we will no longer have a choice; we will have to find ways of using them anyway. Fortunately, several types of industrial waste allow for the recycling of aggregates that could generate pathologies.”
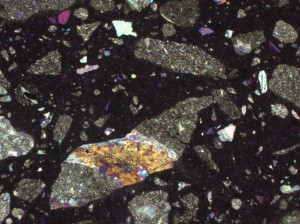
An example of microscopy applied to cementitious materials: a thin section of concrete. The colored components are the aggregates; the black part is the cement paste. The use of traditional optical microscopy (thin petrographic sections) makes it possible to compare the different components, thus facilitating their identification.
Prior research is required in order to find the right concrete formulation to match the intended use. “An extremely precise characterization of the recycled aggregate will be required before it can be integrated into new concrete.” Vincent Thiéry works on characterizing the materials, both natural and recycled. In other words, he uses microscopic observation to interpret the arrangement and properties of the minerals that compose the materials. “We know that in certain aggregates, we will need to look for a specific type of mineral, in a specific form, to determine if there is a risk of the concrete developing a pathology.”
The laboratory has also developed an experimental method based on the dissolution of the cement paste hardened in salicylic acid to measure the percentage of cement in the recycled concrete. The lab features a mechanical characterization center and a digital simulation center.
Partnerships to move from fundamental research to applied research
The EcoSed (Sediments in a Circular Economy) Industrial Chair, launched in April 2014 by Mines Douai, will carry out partnership-based research over a 5-year period on the management of dredging sediments (ports and canals). The tonnages are significant – around 50 million metric tonnes per year in France. “It involves more fundamental aspects, like sediment characterization, before moving towards extremely practical and applied aspects”: developing materials, improving knowledge of sediment-based concrete, and improving knowledge of their behavior in road geotechnics, etc. It is one of the Civil and Environmental Engineering (GCE) department’s flagship projects. It is also participating in the national Recybéton project, which studies the use of materials from concrete recycling sites through experiments in the laboratory and at experimental construction sites.
Leave a Reply
Want to join the discussion?Feel free to contribute!